Functionalisation of FLM (3D-printed) plasticcomponents by means of thermal spraying
Authors: Prof. Dr.-Ing. Dipl.-Wirt.Ing. Wolfgang Tillmann, M. Sc. Christopher Schaak
Plastics stand out due to their low densities and good processabilities and are therefore predestined for lightweight construction. However, the application of plastics is restricted by the low thermal and mechanical strengths. In this respect, the properties are extremely dependent on the utilised plastics and on any reinforcements, e.g. in the form of fibres. The additive fabrication processes are opening up the possibility of manufacturing totally new components and subassemblies with plastics or metals and have therefore aroused rising interest from industry and research for some time. In this case, the interest goes beyond the pure fabrication of prototypes and attention is focusing on series production. Fused layer modelling (abbreviation: FLM) is an established additive fabrication procedure (3D printing) in which a plastic filament is melted completely and applied in lines through an extruder nozzle. This process is repeated layer by layer until the component is built up completely. Within the framework of the investigations, the FLM printing process was used in order to manufacture specimens made of polyamide (FFF nylon) and PLA (polylactide). The surface shapes of the specimens were characterised and the coating was subsequently carried out by means of arc wire spraying in order to functionalise the surfaces of the manufactured lightweight plastic structures. The coated specimens were prepared metallographically and investigated. In this respect, particular attention was paid to the substrate/coating interface and to the integrity of the lightweight structures.
Pages: 122 - 128
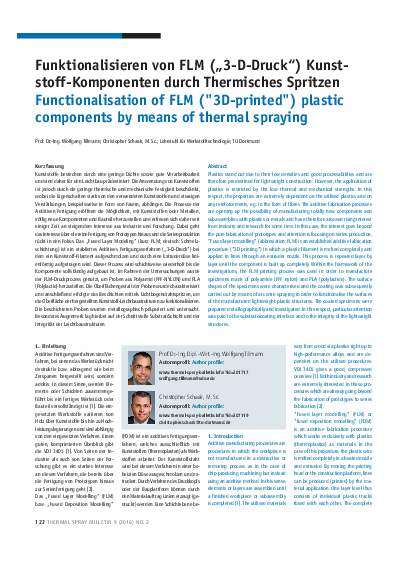
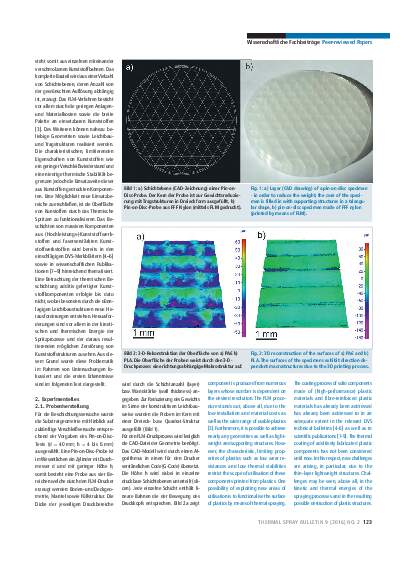
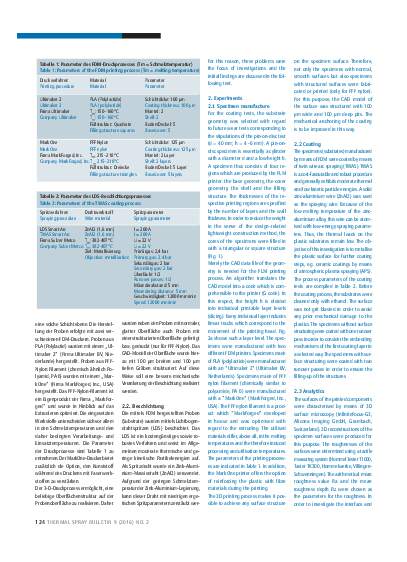
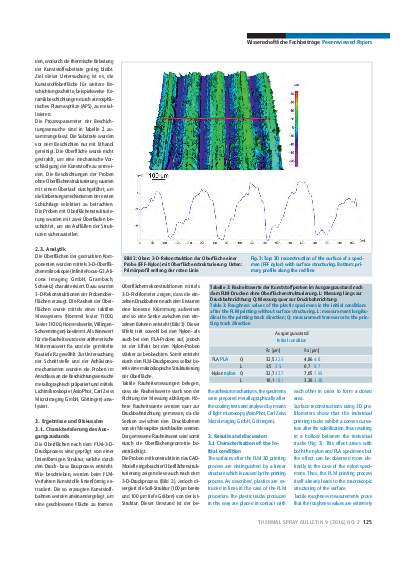
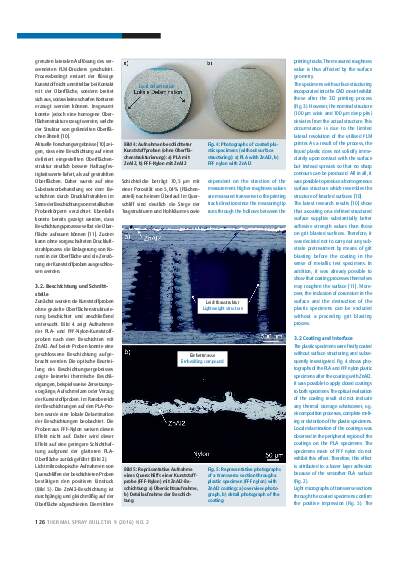
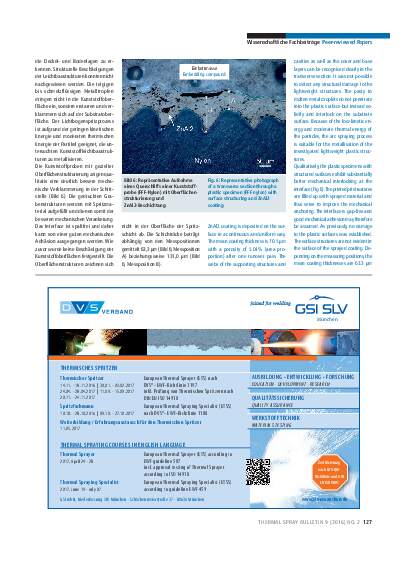
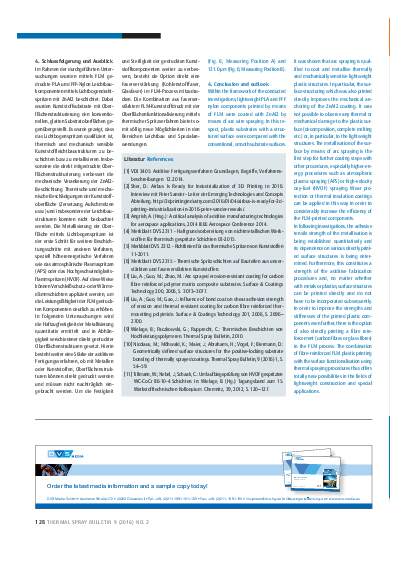
Order this article as a PDF for 8.00 Euro. Send us a short e-mail with your details.
An active subscription enables you to download articles or entire issues as PDF-files. If you already are a subscriber, please login. More information about the subscription