Application of superabrasive hard materialmetal matrix composite systems by means ofthermal spraying
In the application field of the processing of natural stones and concrete, the hardnesses of the materials mean that stringent requirements are set on the utilisation behaviour and service lives of the tools to be used.The materials primarily utilised here are silicon and tungsten carbides, cubic boron nitride and diamond in grain sizes between 250 µm and 350 µm which, in a metal-bound form on carrier materials,
represent the functional coat of the processing tools. Until now, these hard material metal matrix composite systems (MMCs) have been manufactured using the brazing surfacing and sintering processes whose disadvantages are obvious: Brazing-on is an expensive process due to a complicated and often manually executed positioning process of the hard particles whereas the sintering of hard materials in a matrix entails restrictions in the tool geometry. Both processes are characterised by the high complexity of the production and worn tools can no longer be straightened. In contrast, the utilisation of thermal
spraying processes promises the easier and more cost-favourable fabrication and reconditioning of highly abrasive-resistant grinding tools for the processing of stones. The investigation of the suitability of both the higher-kinetic thermal spraying processes HVOF (high-velocity oxy-fuel spraying) and D-Gun (detonation flame spraying) for the manufacture of such abrasive composite material coats is the subject of this article.
Pages: 74 - 79
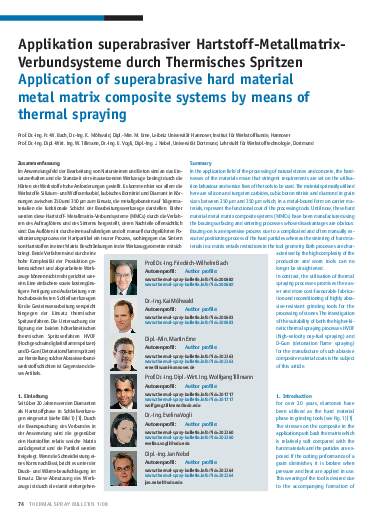
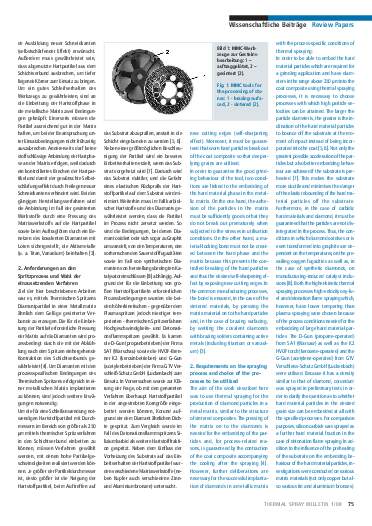
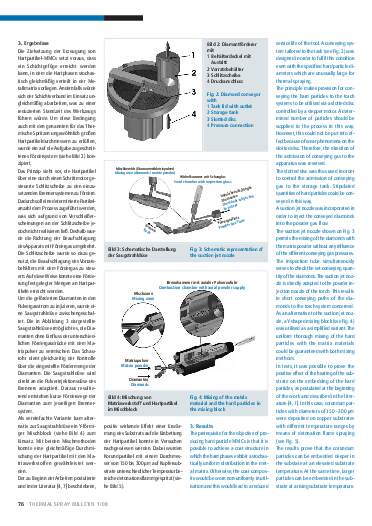
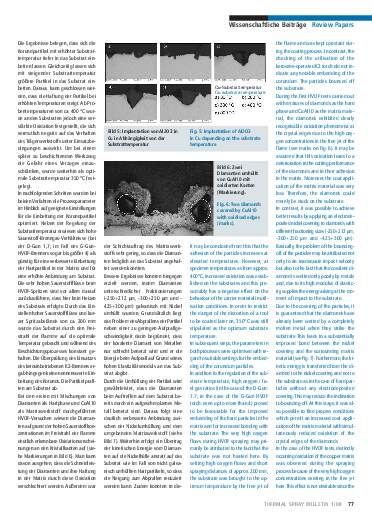
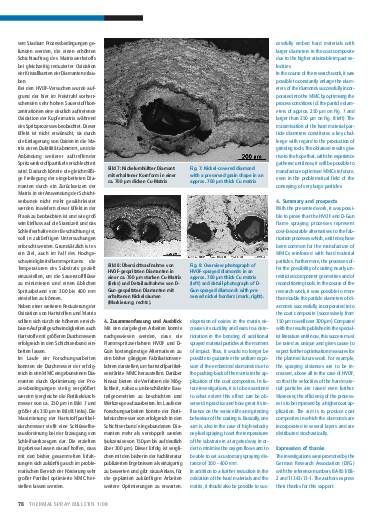
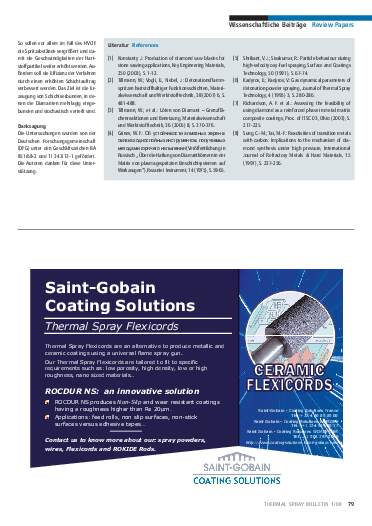
Order this article as a PDF for 8.00 Euro. Send us a short e-mail with your details.
An active subscription enables you to download articles or entire issues as PDF-files. If you already are a subscriber, please login. More information about the subscription